「滑りを良くする!」テフロン™フッ素樹脂(PTFE)の低摩擦性を解説
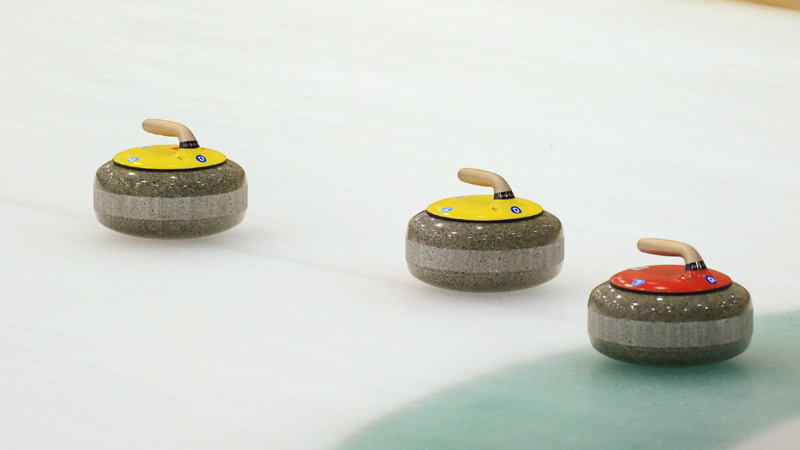
この地球上で物を動かしたり搬送したりするとき、摩擦の働きを無視するわけにはいきません。摩擦を小さくすることで、軽い力で、早く物を動かすことができます。また擦れ合うときに物質が削れたり減ったりする現象を抑えられます。
この記事では、摩擦を低減する潤滑材料としても知られているフッ素樹脂(PTFE)のもつ低摩擦性について、詳しく解説します。
社内回覧やチーム共有に最適な解説資料を無料でダウンロードいただけます。ぜひご活用ください。
目次 [閉じる]
摩擦とは?
「摩擦」とは、接触する2つの固体が相互に運動する際に、表面に生じる抵抗のことです。
物体が動くところでは、多くの場合で摩擦が関係しています。例えば走行中の自動車はブレーキパッドの摩擦により減速します。またスポーツにも、カーリングなど摩擦が深く関係するものが数多く存在します。
その一方で、摩擦は摩耗の原因ともなり、材料表面の肉減りなどの現象を引き起こします。
摩擦の低減対策
摩擦を低減させる手法のひとつに、潤滑材料の利用が挙げられます。
潤滑材料には、気体、液体、固体のものがあり、比較的扱いやすい液体がよく利用されます。近年ではSDGsへの取り組み、すなわち環境改善の観点から、飛散性や化学物質を有する材料の使用を控える場合があります。
■おもな潤滑材料
気体 | 空気、不活性ガス(ヘリウム、アルゴンなど) |
---|---|
液体 | 油、エマルジョン、水溶液、グリース |
固体 | 二硫化モリブデン、グラファイト、PTFEなど |
ここでは固体潤滑材料、なかでも周囲の環境への影響がより少ないフッ素樹脂(PTFE)に注目して解説します。
フッ素樹脂(PTFE)の低摩擦性とは
物体表面に生じる摩擦力の大きさは、よく摩擦係数という指標で表されます。静止しているものを動かそうとするときの摩擦係数を「静摩擦係数」、動いているときの摩擦係数を「動摩擦係数」といいます。
フッ素樹脂(PTFE)の摩擦係数は、静摩擦係数・動摩擦係数ともに、他のプラスチックと比較して非常に小さくなっています。フッ素樹脂のFEPやPFAと比較しても、PTFEの摩擦係数は最も小さいです。そのためフッ素樹脂(PTFE)は低摩擦性に優れ、潤滑用途で多く利用されています。
潤滑材としてのPTFEのメリットには
- 潤滑油やグリスのように周囲を汚染しない
- 相手材を着色させない
- さまざまな環境で使用できる
などがあります。
■フッ素樹脂の静摩擦係数(弊社測定値)
静摩擦係数 | |
---|---|
PTFE | 0.06 |
PFA | 0.08 |
FEP | 0.14 |
フッ素樹脂(PTFE)が低摩擦性に優れる理由
それでは、なぜフッ素樹脂(PTFE)は低摩擦性に優れる(摩擦係数が小さい)のでしょうか?
その理由を、分子構造に着目してみていきましょう。
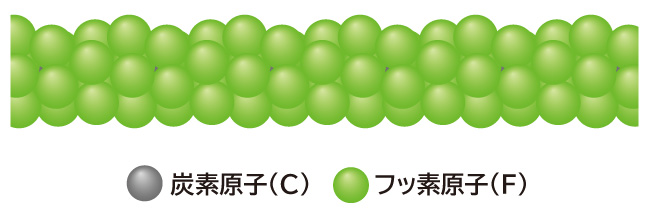
PTFEの分子構造は炭素原子のまわりをフッ素原子が隙間なく取り囲んだ構造になっています。
PTFE分子表面の滑らかさ
PTFEの分子構造は、化学的に対称で直鎖状です。そのため分子表面の凹凸が少なく、全体的に滑らかな表面をしており、低摩擦性に優れると考えられています。
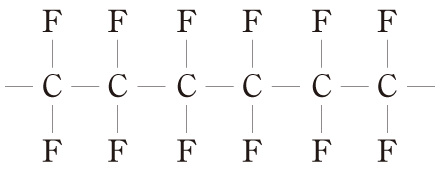
原子間結合力の強さ
PTFE分子内の原子間結合力が非常に大きいため、相手材分子との分子間力(引き合う力)が小さくなり、凝着しにくいことも滑りやすい理由といえます。

ラメラ構造とPTFEの移着
PTFEは結晶性プラスチックに分類され、結晶層と非晶層が積層したラメラ構造(板状結晶)をしています。PTFEが滑りやすい理由として、結晶層のラメラが非晶層との境界部分でせん断(ズレ)を起こしやすいためといわれています。
また、PTFEの表面で摩擦が発生した際、結晶ラメラが相互に滑りを起こし、相手材に移着することで非常に薄いPTFE膜を形成するとされています。肉眼では確認できないほどの非常に薄いPTFE層が形成されることで、摩擦界面が「PTFE 対 相手材表面」から「PTFE 対 PTFE」に変化することも低摩擦性に優れる理由のひとつです。
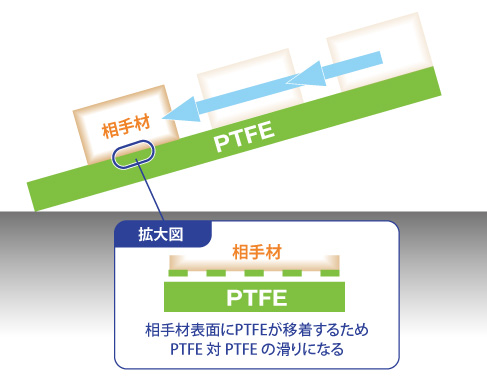
フッ素樹脂の低摩擦性を利用してできること
フッ素樹脂の低摩擦性は、無給油潤滑を可能にし、潤滑油やグリスが使用できない環境で多く利用されています。
また、耐熱性や耐候性などにも優れるため、さまざまな環境で使用することができます。例えば免振装置のスライディングパットの場合、すべり性に加えて耐候性なども必要になります。ご家庭で使われるアイロンの熱板では、フッ素樹脂コーティングが加工され、滑りの良さと熱に強い性質(耐熱性)が活用されています。
吉田SKTでは低摩擦性に優れるフッ素樹脂コーティングの加工はもちろんのこと、低摩擦性を利用した滑り性に優れる表面処理(コーティング)の開発も行っております。詳しくは下記リンクよりご覧ください。
社内回覧やチーム共有に最適な解説資料を無料でダウンロードいただけます。ぜひご活用ください。