樹脂成形とは?基本事項から射出成形などの成形方法までご紹介
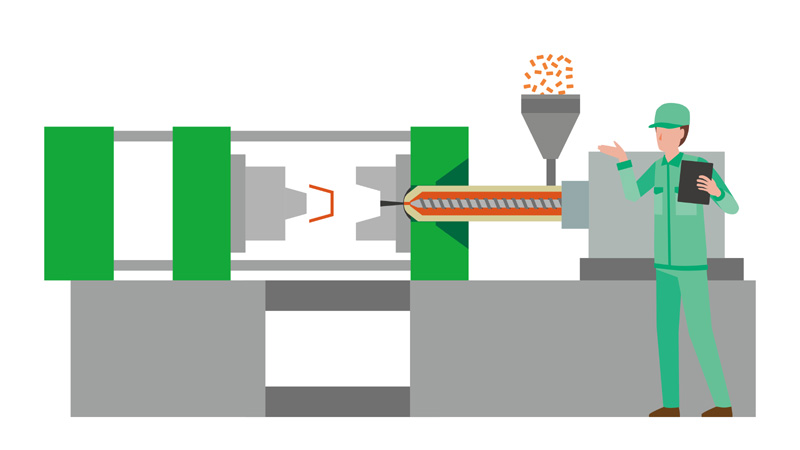
樹脂成形は、熱可塑性樹脂や熱硬化性樹脂を材料とした成形品の生産に使われる非常に重要な技術です。
この記事では、樹脂成形の基本事項や成形手法、射出成形の実際の過程や課題点などについて解説します。
目次 [閉じる]
樹脂成形とは
樹脂成形とは、溶かした樹脂を型に流し込んで望ましい形にした上で、冷却して製品を作る方法です。樹脂は粉末や粒状のものを使い、加熱して溶かしながら金型に流し込んだり、押し込んだりします。簡易に見えますが、樹脂の種類や用途に合わせて金型を調整するような細かな条件設定が必要です。
樹脂成形には多くの手法があり、製品の形状や用いる材質に合わせて最適な成形法を選択します。
熱可塑性樹脂の成形
熱可塑性樹脂は、加熱すると柔らかくなり、冷やすと硬化する樹脂です。融解温度が比較的低い素材もあるため加工も簡単で、大量生産に向いています。リサイクルが可能な点も特徴です。
ただし汎用プラスチックに分類されるものは高温に弱く機械的強度も比較的弱いため、用途は限定されます。強度と耐熱性が要求される場合は、エンジニアリングプラスチックや熱硬化性樹脂がおすすめです。
ポリエチレンやアクリルなど、一般的によく見るプラスチック材料はほとんどが熱可塑性樹脂です。加工がしやすいため、成形には融けた樹脂を型に流し込んで冷却するシンプルな手法が用いられます。
熱硬化性樹脂の成形
熱硬化性樹脂は、加熱すると分子の間に架橋構造が生まれ、高い耐熱性や強度をもつ樹脂です。架橋とは、分子間に橋が架かったような構造で分子が連結されることです。
一度固くなった樹脂は加熱しても再び柔らかくならないため、リサイクルには向いていません。また、その硬さのために衝撃に弱い点もデメリットです。一方で耐熱性が高く、たわみや歪みについても優れた耐性をもっているため、熱硬化性樹脂でしか対応できない用途も多数あります。
耐性を得るためには複雑な硬化プロセスがあり、安定生産を目指すには、さまざまな工夫が必要です。
樹脂成形の主な方法
樹脂成形には数多くの手法があるため、ここでは代表的な成形方法について解説します。
それぞれの手法ごとに、得意な分野や成形できる樹脂の種類があります。各成形方法の原理や特徴をふまえて、用途に合った方法を選択することが重要です。
射出成形
射出成形は、最も一般的な方法です。金型に加熱した樹脂を充填し、圧力をかけて形成します。一度金型を作っておくと同じ形の製品を早いペースで生産できることが特徴です。
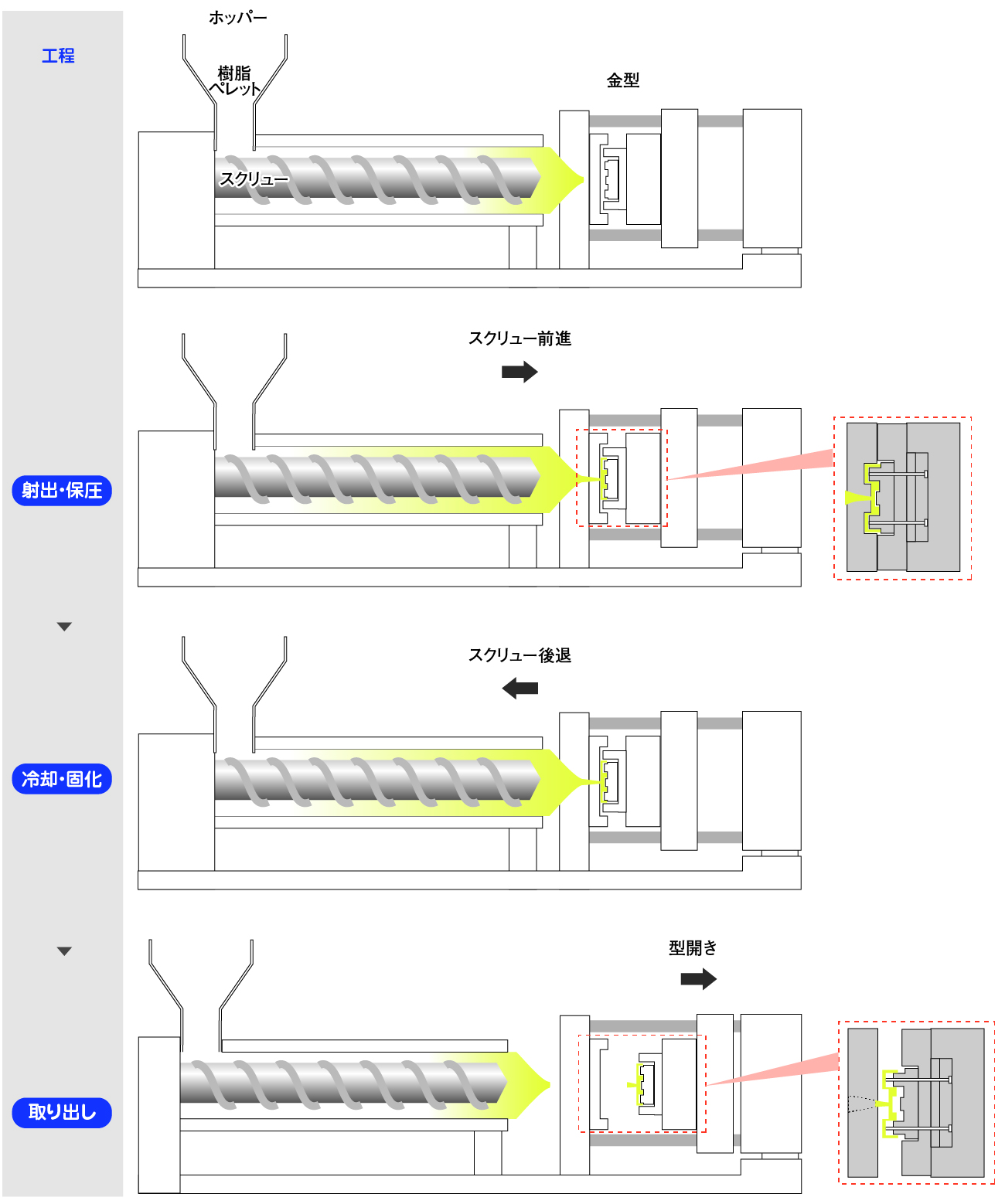
ブロー成形
ブロー成形は、加熱して柔らかい状態の熱可塑性樹脂を金型に入れ、内部から空気で膨張させて金型に押し付けるように型をとる成形手法です。準備が簡単で工程も少なく済むことや、金型の費用を下げられ、製品を安価に製造できる点がメリットです。
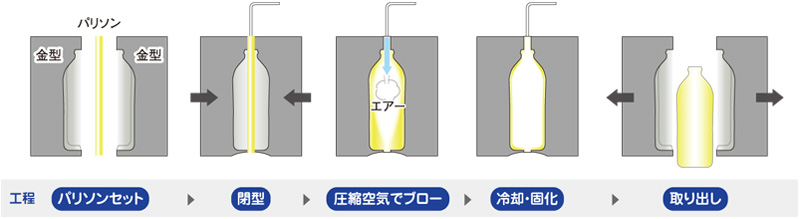
ただし、内部の形状や厚みなどを制御することは難しく精度が出ないことや、中空構造の部品しか作れないなどの欠点があります。
真空成形
真空成形は樹脂のシートやフィルムを材料に、樹脂成形を行う手法です。シートを金型に貼り付け、金型に開いた穴から空気を吸引すると、金型にシートが吸着します。
金型が片面だけで済むため、製作費用の安さが特徴です。少量で多種を生産する場合はもちろん、連続した生産も可能なため大量生産に向いており、さまざまな製品に利用されています。
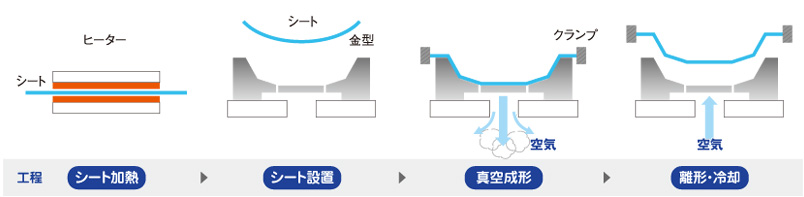
押出成形
押出成形は、加熱して柔らかくした樹脂を、ダイという金型に加圧して通すことで成形し、冷却してから切断する成形手法です。
特殊な形の製品に使う成形方法で、形状は制限されますが、フィルム・シート・チューブなどの大量生産に適しています。金型を取り替えるだけで形状の切り替えができ、他に大規模な変更の必要がない点もメリットです。
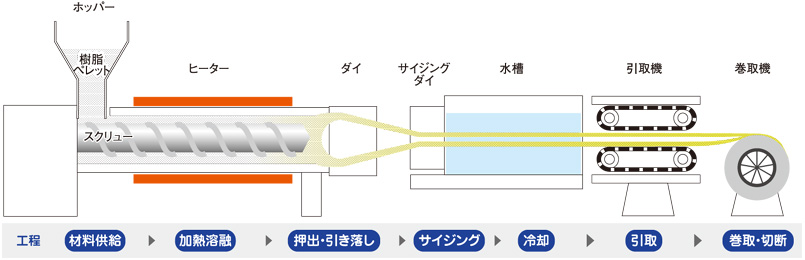
カレンダー成形
カレンダー成形とは、加熱した2本のローラーの隙間から溶かした樹脂を下に出しながら熱延伸ロールで延ばす手法です。フィルム状の製品を成形する手法であり、押出成形に似ています。押出成形と違って口金(金型)が不要です。
設備が大規模になるために少量の生産には向かず、平らな製品以外は作れません。ただし形状が合えば連続して生産できるため、大量生産向きの手法です。
圧縮成形
圧縮成形は多くは熱硬化性樹脂の成形で利用されます。熱した金型に成形する樹脂を入れ、そこからさらに圧力をかけることで樹脂の硬化を促します。高圧をかけるため高密度で頑丈な製品になり、厚みのある製品の成形に適しています。
ただし、射出成形と比べて成形スピードが遅く大量生産にあまり向いていない点と、2次加工が必要な場合があります。大きなバリがロスとして生じる点が課題です。
トランスファー成形
トランスファー成形は、圧縮成形のやり方を改良し、量産性を高めた成形法です。密封された金型に樹脂を注入する構造を追加し、加圧しながら注入して硬化させます。
金型の構造は複雑になりますが、加圧による高密度さと頑丈さを保ち、工程を短縮して量産性が高められています。インサート部品や小型の電子部品など、精度や耐久性が求められる製品に最適です。
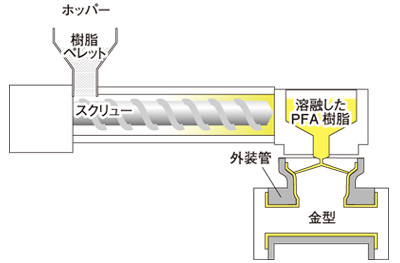
積層成形
積層成形は、樹脂が染み込んだ紙や布を多数重ね合わせておき、それらを加熱、加圧して1つの製品にする成形手法です。形状が複雑な製品には対応が難しく、また設備が大規模になりやすいデメリットがあります。
ただし、樹脂にガラス繊維を組み合わせてプラスチックの強度を向上させることが簡単に行えるため、強化プラスチックなどの製造に使われています。
射出成形とは
射出成形は、溶かす・流す・固めるという3つの工程から成り立っています。
樹脂の成形法としてもっとも一般的ですが、不良品を出さずに大量に成形を行うためには細かな調整が必要です。
最も利用されているプラスチック成形
射出成形はプラスチック成形の中でもポピュラーな手法であり、さまざまな製品の成形に使用されています。
加熱したシリンダーに流し込まれた樹脂が、解けながらスクリューによって先端に運ばれ、必要量が貯まると加圧されて金型に流し込まれます。冷えて固まったら完成です。
金型を使用することで同じ形状の製品を短時間に多数生産できます。非常に効率的な成形方法であり、その生産性の高さが最大のメリットです。
高品質で大量生産が可能
射出成形は、金型を作成すれば複雑な形の製品でも高い品質で素早く作れる方法であり、速いものでは数秒で1個の割合で生産が可能です。
ただし、金型を造る費用が非常に高く、少数生産には向いていません。また、製品の品質を保ち、形状を安定させて気泡を発生させないためには、設備のセッティングや注入圧力などの細かな調整が必要です。
大量生産を目的とする手法ですが、その実施には技術的な熟達が求められます。
射出成形には金型が重要
射出成形ではプラスチックを充填する際に高圧がかかります。このため、射出成形の金型には、高圧に耐えられる耐性と精密さが必要です。大きなパーツを作る場合、かかる圧力が約3,000トンに達するケースもあります。
充填圧力は、シリンダーのスクリューの回転数やシリンダーの背圧で調整が可能です。圧力の調整が上手くいかない場合、気泡が発生・混入したりガスの圧力で背圧が押し負けたりするなど、失敗の原因となります。
よくある成形不良に注意
射出成形は高品質な製品を大量に生産できる一方で、成形不良について注意が必要です。
よくある成形不良として、ヒケやボイド、ソリによる変形などが挙げられます。
- ヒケ:溶融している樹脂が冷えるときに収縮によって体積が変わり均一に冷却しないことで表面がくぼんでしまう現象
- ボイド:内部が遅れて硬化することで、内部に収縮が起きて樹脂内部に気泡ができてしまう現象
- ソリ:樹脂の収縮と温度差によって製品が本来の形状より反ってしまう現象
- 脱型不良:金型に樹脂がはりついてしまい、うまく脱型できない事象
ヒケ、ボイド、ソリなどは、溶けた樹脂が冷却する際に起きるため、設計段階から成形品の肉厚を検討したり、金型温度の設計を見直す必要があります。一方で、脱型不良は成形条件や金型形状の見直し以外に、離型剤の使用や離型コーティングを活用することで解決できる場合があります。
まとめ
樹脂成形は現代の製造業に不可欠な技術です。本記事では、熱可塑性樹脂と熱硬化性樹脂の特性、そして射出成形を中心とした様々な成形方法について解説しました。射出成形は高品質な製品を大量生産できる反面、金型製作に高コストがかかり、成形不良を防ぐための細かな調整が必要です。各成形方法にはそれぞれ長所と短所があり、製品の要件に応じて最適な手法を選択することが重要です。
吉田SKTは、成形金型への表面処理事例が豊富で、特に離型処理を得意としています。当社は豊富な経験を活かし、お客様のニーズに合わせた最適なコーティング・表面処理を提供いたします。成形のトラブルや金型へのコーティング処理など、樹脂成形に関する問題でお悩みの方は、ぜひ一度ご相談ください。
弊社の技術営業員が個別にご対応させていただきます。下記お問い合わせフォームよりお問い合わせください。