熱溶着とは?仕組みや分類、メリット・デメリット、活用例を解説
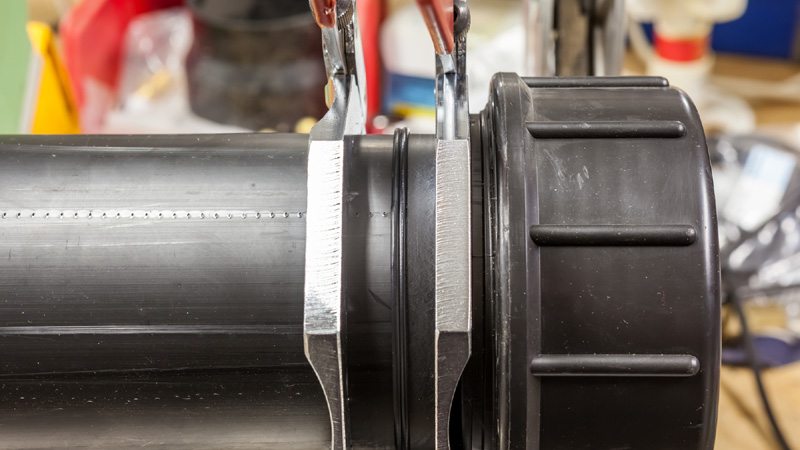
溶着とはさまざまな素材を接着する際に使われる技術で、そのうちメジャーな方法の1つが熱溶着です。この記事では、熱溶着の仕組みや分類などの基礎知識に加えて、どのような素材に適しているのか、どのような場所で活用されているのかを解説します。
目次 [閉じる]
溶着についての基礎知識
熱溶着はさまざまな場面で活用されていますが、具体的にどのような加工法を指すのでしょうか。
ここでは、熱溶着を含む「溶着」という技術全般に対する基礎知識を紹介します。また、混同されやすい用語との違いについても解説します。
溶着とは
溶着とは、熱可塑性の樹脂素材(プラスチック)や非鉄金属の接合を目的とした加工法全般を指す言葉です。非鉄金属とは鉄以外の金属をまとめて指す言葉で、銅や亜鉛、アルミニウムやチタンなどさまざまな金属が含まれます。
溶着は加熱・加圧・冷却のプロセスを踏んで行われますが、それぞれのバランスを考慮して作業する必要があります。これらのバランスが崩れると、溶着不良や美観が悪くなることがあります。
また、溶着における加熱方法には外部加熱と内部加熱の2種類があります。これらはそれぞれ適した素材や活用される場面が異なります。
溶接との違い
溶着と混同されやすい加工法として、「溶接」があります。溶接とは、母材や溶加材を溶かして金属を接合する技術です。
溶着したものと溶接したものは見た目に違いがあります。一般的に、溶融部を判別できる方が溶接、判別できない方が溶着です。ただし、英語ではどちらも「Welding」と呼んで区別していないことが多いため、海外の本や資料を読む際はどちらの意味で用いられているのかを確認しながら読解する必要があります。
熱溶着の仕組み
熱溶着は溶着方法のうち、外部からの加熱によって部品・素材を溶かすことで溶着する方法を指します。樹脂溶着の方法としては昔から用いられている加工法で、高い強度での接着が可能です。
なお、「熱溶着」と呼ばれる中でも加熱方法によってさらにいくつかの種類に分類できます。さまざまな道具を用いた方法があり、特に熱板式・熱風式・コテ式の3つがよく用いられる代表的な熱溶着の方法です。適した厚みや形状が加熱方法によって異なるため、素材や目的に合わせた方法を選ぶ必要があります。
熱溶着の分類
前述の通り、熱溶着は加熱に使う道具によっていくつかの種類に分けられます。それぞれに異なる利点があり、加工後の仕上がりにも差が生じるため、目的に応じた方法を選ぶことが大切です。
ここからは代表的な熱溶着方法と、それぞれの特徴や注意点について解説します。
熱板式溶着
熱板式溶着とは、熱した板を素材同士の間に挟み込み、溶着する面を熱してくっつける溶着方法です。熱板で直接溶かす接触タイプと輻射熱を利用して溶かす非接触タイプに分けられます。導入費用が比較的安く、大きな素材や立体的な素材も溶着できることが利点です。
ただし、バリ(余肉)が出やすいほか、電子部品が入っているものや精密機器は熱の影響を受けるため溶着できません。また、熱板に直接触れる方法の場合は樹脂が糸引きを起こす可能性があるため、適切な離型処理が大切です。さらに、必要以上に加熱すると気泡が生じ、接着不良が起こる可能性もあります。そのため、熱板式溶着においては熱板の温度や距離、加熱時間などの調整が重要です。
熱風式溶着
熱風式溶着は、溶着するものの間に熱風を吹きつけ、ローラーを用いて加圧・溶着する方法です。
曲線形の素材にも対応できることや部品の厚さに左右されずに溶着できることが利点で、養生シートや防護服などさまざまな用途に活用されています。
コテ式溶着
コテ式溶着とは、コテ(加熱板)を使って熱し、ローラーで加圧・溶着する方法です。熱溶着では比較的仕上がりが綺麗なほか、ほとんどの熱可塑性フィルム・シートを溶着できることが利点です。
また、コテ式溶着であれば素材の厚さに関係なく溶着できます。これは、溶着面に直接加熱板を当てるためです。
摩擦熱を用いた熱溶着
代表的な熱溶着方法は先に紹介した3つですが、それ以外の熱溶着方法として、摩擦熱によって接着する方法があります。スピン溶着は溶着物の面同士を合わせ、高速回転させることで生じた摩擦熱によって溶融・溶着する方法です。消費電力が少なく気密性に優れるほか、内部部品への影響が少ないことも利点といえます。
また、溶着物を接触させた状態で振動させて振動する時の摩擦熱によって溶着する方法もあり、振動溶着と呼ばれます。
その他の溶着の種類
溶着には熱溶着以外にも種類があり、それぞれに利点があります。ここからは、熱溶着以外の溶着方法とその特徴、利点について触れます。素材や用途の関係で熱溶着による加工が難しい場合に選択肢として検討するとよいでしょう。
高周波溶着
高周波溶着は、高周波(電磁波)エネルギーの電界作用を用いて被加熱物を内部から発熱させる溶着方法です。溶かしたい部分だけピンポイントで加熱できることが特徴で、加熱が短時間で済みます。また、溶着しない部分への熱の影響が少なく、美しい仕上がりになることや強度に優れることも利点です。
ただし、電磁波を利用するため周辺設備への電磁妨害の有無や、関連法規などを使用前に確認する必要があります。
超音波溶着
超音波溶着は、超音波振動を共鳴体(ホーン)から被加熱物に伝え、内部に発生する摩擦熱で接合する溶着方法です。さまざまな種類の熱可塑性プラスチックを加工できるため、さまざまな場面で用いられます。また、溶着時間が短く装置本体やランニングコストも安価なため、費用や所要時間を抑えられます。
装置が安価なだけでなくコンパクトであまり場所を取らないことも利点です。ただし、大きな部品や立体的な形状のものの溶着が難しいという注意点もあります。
熱溶着のメリット
さまざまな溶着方法から熱溶着を採用することには、どのような利点があるのでしょうか。ここでは、ほかの溶着方法と比較した際に熱溶着が優れているといえる点をいくつか紹介します。
溶着できる面積が広い
熱溶着は外部から加熱することで部品を温めるため、広い範囲を一度に加熱できます。大型・小型の部品を問わず溶着できることが大きな利点です。
立体的な部品の溶着にも適しており、さまざまな場面において活用が可能です。複雑な形状の部品を溶着する機会がある場合は、熱溶着が適しています。
費用が安い
熱溶着は熱で溶かして素材を溶着する、シンプルな方法を採用しています。装置も比較的単純な構造で、超音波装置や電磁波装置よりも導入費用が安価です。また、熱板溶着は一般的には消耗材を必要としないためランニングコストが少なく、長い目で見ても費用を抑えられます。
これらの理由から、費用を抑えて溶着用の装置を導入したい場合は、熱板溶着がおすすめです。
強度が高い
熱溶着は冷え固まるまで加圧することから溶着後の強度が高く、気密性を重視する部品に向いています。また、立体的な形状であっても対応可能なため、他の方法では加工が困難な部品も接着可能です。部品のサイズが大型か小型か、形状が複雑かどうかというような要因を問わずしっかり溶着できるため、さまざまな場面に対応できます。
熱溶着のデメリット
ここまで熱溶着の利点を紹介してきましたが、状況によっては熱溶着を用いない方がよい場面もあります。
ここからは、熱溶着を用いる際のデメリットを紹介します。作業の前に熱溶着を用いてよいかどうかを確認しましょう。
溶着部以外も加熱される
熱溶着は加熱する範囲がほかの溶着方法よりも広いため、加熱しなくてよい所にも熱が伝わります。また、内部加熱の方法よりも加熱にかかる時間が長く、素材に影響が出る可能性もあります。
溶着する部分近くの狭い範囲にだけ熱を加えたい場合には、超音波溶着や高周波溶着などの内部加熱が適した方法です。
装置の管理に気を配る必要がある
外部加熱を用いる熱溶着は、作業時間を推定する際に予備加熱にかかる時間も考慮しなくてはなりません。
また、作業中は常に適切な温度を保たなくてはならないことも覚えておいたほうがよい点です。加熱しすぎたり、温度が低かったりすると接着不良の原因になり得ます。
さらに、加熱後に加圧しすぎるとバリ(余肉)が多くできやすくなるため、こちらも気をつける必要があります。
特に熱板を利用した溶着では素材や方法によって、糸引きやはりつきのトラブルが生じることがあります。このような時は熱板に離型性の高い表面処理を施す必要があります。
参考記事:【事例】ポリエチレン(PE)製容器の溶着糸ひき防止を実現する表面処理
参考記事:【新開発】表面処理CHC(セラミックハードコート)のご紹介
熱溶着の活用例
熱溶着が用いられる具体的な事例としては、以下のようなものが挙げられます。
- 貯水タンク
- 自動車の樹脂タンクやテールランプ
- バッテリー
- 防炎やテントに用いられる樹脂シート類
- 携帯電話のケース
- 文房具のケース
- 家電・家庭用品
- 自動車部品
- 防護服 など
これらはほんの一例ですが、これを見ても分かるように、熱溶着は日常の身近なところで活用されています。気密性・水密性に優れるため、特に自動車部品やタンク類には高い頻度で活用されています。
まとめ
吉田SKTでは、熱溶着時の樹脂の糸引きや熱板への素材の付着というようなトラブルを改善する表面処理が可能です。こちらのページでは多数の事例を紹介しています。
熱溶着工程を改善したいかたや、加熱板などへの表面処理・コーティングをご希望のかたはぜひ吉田SKTにお問い合わせください。環境や目的に応じたご提案をさせていただきます。