半導体の製造プロセスを徹底解説!半導体の仕組み・製造の流れの理解をサポート
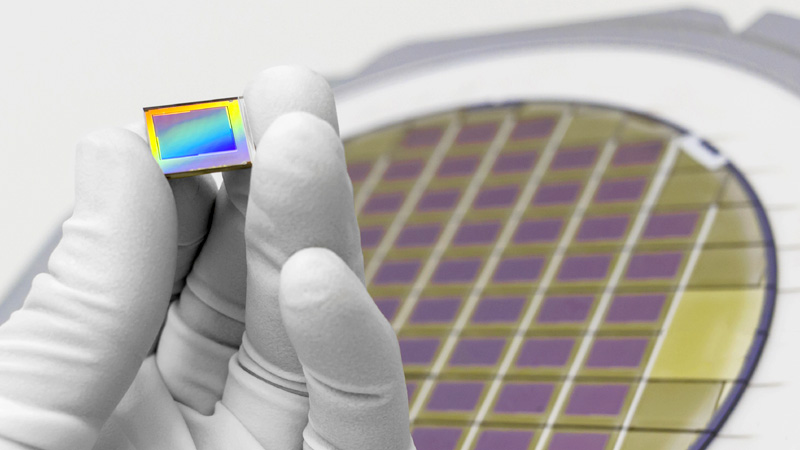
こんにちは。「吉田SKT」ブログ編集チームです。
半導体の需要は非常に高まっており、人々の生活になくてはならないものといえます。しかし、半導体の概要や製造のプロセスを知らない人は多くいます。
この記事では、半導体の製造プロセスを解説しているため、半導体の理解を深めることが可能です。半導体製造における課題、今後に必要な次世代半導体についても紹介しているので、ぜひ参考にしてください。
半導体の製造プロセス
半導体は、複雑な工程を経て作られています。ここでは、半導体の製造プロセスについて解説します。
半導体は3つのプロセスで製造される
半導体の製造は、設計・前工程・後工程の3工程で行われます。ここでは、それぞれの工程について解説します。
設計
設計は、半導体に必要な回路とパターンを構築する工程です。シミュレーションを通して効果的なパターンを検証し、検証が終わった後は、フォトマスクとシリコンウエハーを形成します。フォトマスクとは、回路パターンを描く透明なガラス板です。トランジスタや配線は細かく、ウエハーへの配置が困難なため、パターンを描いた後にフォトマスクに転写する必要があります。
前工程
前工程は、シリコンウエハーの表面上に電子回路を形成するまでの工程です。シリコンウエハーとは、シリコンから作られた材料基盤です。シリコンウエハーは超高純度の単結晶インゴットを薄く切って作り、1枚のウエハー上に数百個の半導体チップを格子状に並べて形成されます。半導体はシリコンウエハーに複数個の配線回路層を形成し、複数のプロセスを経て完成します。
後工程
後工程は、半導体をウエハーから切り出して製品化する工程です。ウエハーから集積回路を1つずつ切り出し、半導体チップを金属に固定して、配線処理を施した後樹脂で固めて保護します。半導体チップは繊細な製品であるため、検品を行い、検査の基準を満たさないものは不良品として除外されます。
設計
半導体の設計は、回路やパターンを設計した後に、フォトマスクを作成してパターンの転写を行う工程です。ここでは、それぞれの工程で行うことや注意点などについて解説します。
1. 回路・パターンの設計
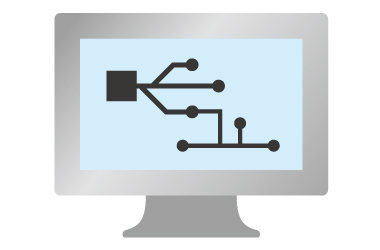
回路・パターンの設計は、半導体が必要な製品の用途に合わせて回路を設計する工程です。半導体チップ上に効果的なパターンを作成するために、シミュレーションを通して繰り返し検証をする必要があります。
2. フォトマスク作成
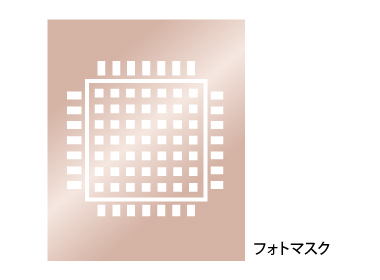
フォトマスクは、回路のパターンを透明なガラス板に描いて作成します。フォトマスクの原版は、シリコンウエハー上にパターンを転写してつくります。フォトマスク作成は非常に細かい作業であるため、コンピュータを使うことが必須です。
前工程
前工程は、シリコンウエハーの作成から回路パターンの作成までの工程です。半導体に複数の配線回路層を作るために、それぞれ細かく分かれたプロセスを実行します。ここでは、前工程の内容について解説します。
1. シリコンウエハーを作成する
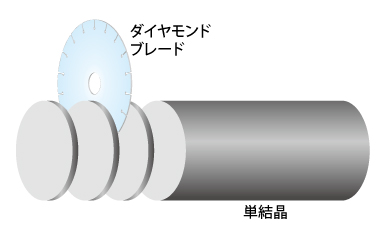
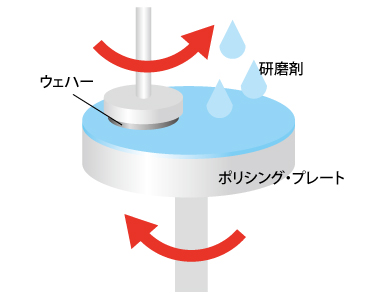
最初にシリコンの単結晶の塊であるインゴットを作成します。シリコンウエハーを作成するために、インゴットは薄く切ります。ウエハーの側面・表裏面は研磨や鏡面化などを行い、微粒子や微細な凹凸を排除することが必要です。
2. シリコンウエハー上に回路パターンを形成する
シリコンウエハー上の回路パターンは、8つの工程を繰り返すことで形成されます。ここでは、回路パターンの形成について解説します。
(1)シリコンウエハー表面の酸化
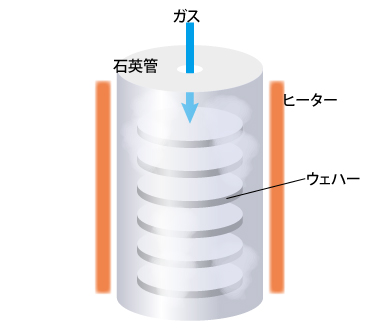
シリコンウエハー表面の酸化は、成膜の工程の1つです。成膜とは、トランジスタや配線などをつくるための層の形成を指します。高温の酸素によって熱酸化したシリコンウエハーは、酸化シリコンの膜を生成し、絶縁層としてトランジスタの構成要素となります。
(2)シリコンウエハー表面の薄膜形成
シリコンウエハー表面の薄膜形成とは、酸化膜の上にアルミニウムなどの金属やガスなどの薄膜を作成することです。薄膜の不要部分の除去を繰り返すと、複数の層が作られます。
(3)フォトレジストの塗布
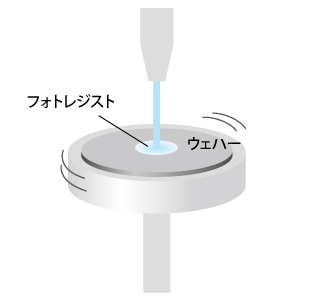
感光剤であるフォトレジストを、ウエハー表面に均一に塗る工程です。フォトレジストの塗布は、導体のパターンを転写するために行います。シリコンウエハーを回転させると、遠心力を活用して均一に塗れます。
(4)フォトマスクのパターン転写(露光・現像)
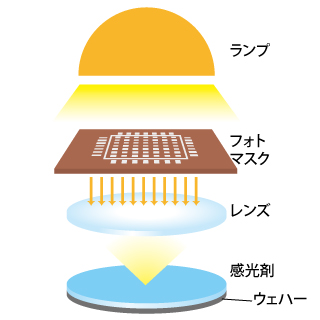
シリコンウエハー上に、フォトマスクのパターンを転写する工程です。パターンの転写は、レンズを通して遠紫外線を照射し、光が当たった部分のレジスト膜を変質させて行います。フォトレジストの露光された部分は、現像液で溶かしてパターンが転写された部分を残します。
(5)エッチング
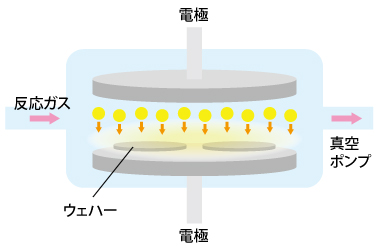
エッチングとは、フォトレジストで形成した酸化膜や薄膜の部分を除去するために、パターンに沿って削り取る作業です。リン酸やフッ素などの薬液をつかって削ることで、回路パターンが形成されます。
(6)フォトレジストの剥離 ・洗浄
フォトレジストは形成されたパターン上に残るため、除去作業を行います。除去の作業を行う際は、薬液に浸けて洗浄します。
(7)イオンの注入
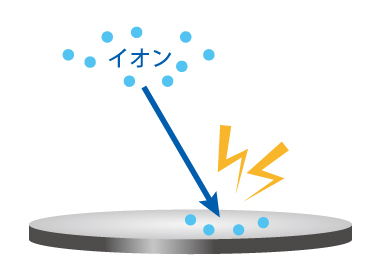
シリコンウエハーに半導体の特性を持たせるために、不純物イオンを注入します。不純物イオンを熱処理すると、半導体の電気的特性を得ることが可能です。リンを添加するとN型半導体が作られ、ボロンの添加でP型半導体が作られます。
(8)シリコンウエハー表面の研磨
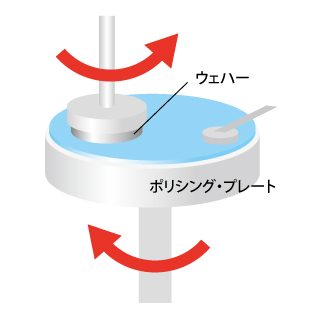
シリコンウエハーの表面は、研磨して凹凸をなくすように平坦化します。シリコンウエハーの表面を再度きれいにした後、次の層の作成を始めます。
3.電極の形成
電極を形成するために、金属をシリコンウエハーに埋め込む工程です。電極を絶縁膜上に引き上げるため、酸化膜にコンタクトホールと呼ばれる穴を開けて、金属部を埋め込みます。
4.検査
シリコンウエハー上のすべてのチップを検査する工程です。チップのキズや汚れ、サイズ、電気的な異常など、問題がないかどうかを確認したうえで、印をつける作業を行います。
後工程
後工程は、シリコンウエハーの切断やチップの分別、固定などの作業から最終確認までを行います。半導体を製品として使用できるように、最終確認が終わるまでは細かな調整が必要です。ここでは、後工程について解説します。
1. シリコンウエハーのダイシング
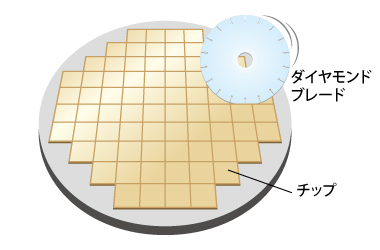
ダイシングは、シリコンウエハーをダイヤモンドブレードなどで切断する工程です。シリコンウエハーをチップに分離して、製品として使われる良質なチップを分ける作業を行います。
2. チップのダイボンディング
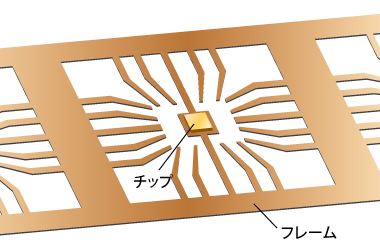
ダイボンディングとは、金属製の枠のリードフレームにチップを固定する作業です。リードフレームとは、薄い金属のチップの支持体です。チップを固定する際は、正しい位置におさめるように注意しましょう。
3. ワイヤーボンディング
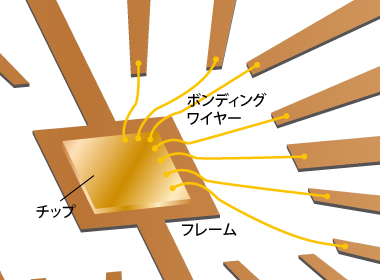
ワイヤーボンディングは、チップとリードフレームを約25μmの金線でつなぐ作業です。ワイヤーボンディングによって、リードフレームを通してチップとの配線ができます。
4. 樹脂のモールディング
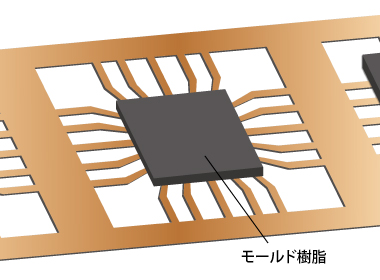
樹脂のモールディングとは、樹脂やセラミックでチップを包み込む作業です。チップは繊細な機器であるため、樹脂でパッケージして、傷や衝撃、ホコリ、磁気などの外部の影響から守る必要があります。
5. 製品化と最終検査
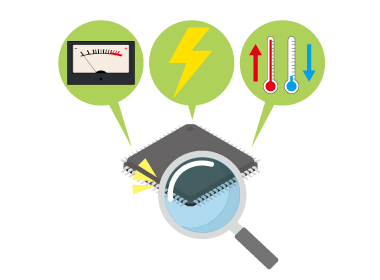
半導体をリードフレームから切断・分離して、半導体製品として成型する作業です。製品の初期不良を減らすため、最終的な検査を行います。たとえば、高温・高圧などの過酷な条件における動作確認のような検査が実施されます。
参考記事:【初心者向け】半導体製造の後工程とは~注目の理由や製造プロセスを解説
半導体の製造における課題
半導体の製造には、環境への配慮や自動化などが求められています。ここでは、半導体の製造における課題を解説します。
クリーンな環境の維持
クリーンな環境とは、一定以上の空気洗浄度を保てる場所のことです。半導体の製造過程に異物が混入した場合は品質に悪影響を与えるため、異物混入防止策の徹底が必要です。ただし、機械の洗浄度の維持や向上は、多額のコストがかかります。
製造工程の自動化
半導体の製造はクリーンな環境で行う必要があるため、なるべく人の出入りを避けなければなりません。人の立ち入りを極力減らすためには、検査工程の自動化が求められます。
高性能な半導体製造装置の必要性
半導体の製造を機械によって自動化する際は、高性能な製造装置が必要です。自動化によって製造できると、人的ミスによる不良品の発生率を抑えられるため、コストを大幅に削減できます。
参考記事:半導体製造装置部品の特徴や種類~一般装置部品との違いや具体例も解説
次世代半導体に求められるもの
半導体の需要が高まっており、技術革新が進んでいます。世界各国の企業が、次世代半導体の開発のために競い合っているのが現状です。ここでは、次世代半導体に求められるものについて解説します。
集積回路の微細化
集積回路の微細化とは、半導体を小さく作ることです。微細化によって半導体を構成する回路が狭まり、密度の高い製品を作れるようになります。微細化した半導体はスマートフォンやパソコンにおいて、大量の情報を処理するチップとして活用することが可能です。
パワー半導体
パワー半導体とは、高電圧・高電流を扱う半導体です。パワー半導体は、電気自動車の充電やモーターの作動、発電、送電などを行う際に、使いやすい形の電力として変換するために活用されています。パワー半導体開発の課題は、高耐圧化と低損失化、漏電の防止と耐久性などです。現在は絶縁破壊強度・熱伝導度が高い「ワイドバンドギャップ半導体」の開発が進められています。
参考記事:パワー半導体とは?半導体との違いや機能、おもな用途などを解説
まとめ
半導体を製造するプロセスは、設計・前工程・後工程の3工程です。半導体の品質を保つために、各工程は細かいプロセスで成り立っています。半導体の製造技術は日々進化していますが、環境への配慮や自動化などの課題があります。企業の製造のプロセスを変更する際は、生産体制の見直しが必要です。
吉田SKTは、表面処理、テフロン、フッ素樹脂コーティングの専門メーカーです。テフロンコーティングのライセンス工場を所持しており、独自技術による表面処理を提供しています。半導体製造装置への実績も多数あります。半導体分野の表面処理をご検討の際はぜひご利用ください。