射出成形とは?基礎知識からメリット・デメリットまで解説
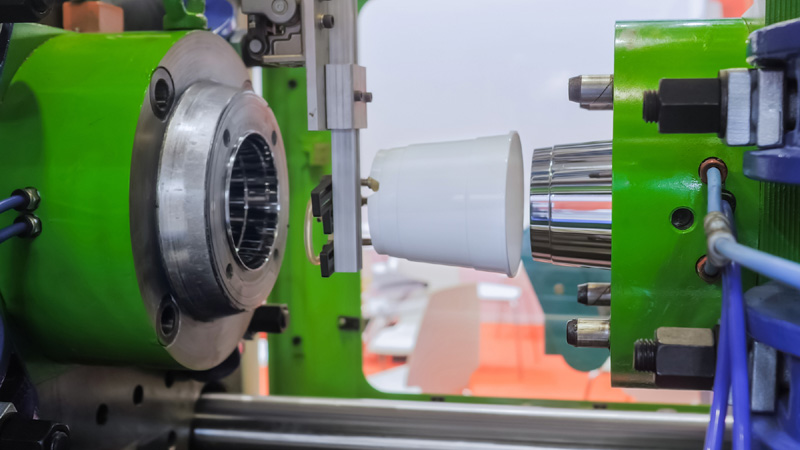
射出成形は、プラスチック製品の製造において最も一般的かつ重要な成形方法です。
この記事では、射出成形の原理からメリット・デメリット、応用技術、さらには業界の最新トレンドまでを詳しく解説します。製造業に携わる技術者や設計者の方々は、製品開発や効率的な生産ライン設計に際して、ぜひご参照ください。
目次 [閉じる]
射出成形の基礎知識
射出成形とは
射出成形(しゃしゅつせいけい、Injection Molding)は、熱可塑性プラスチックや熱硬化性プラスチックを用いて、複雑な形状の部品を大量生産するための製造プロセスです。このプロセスは、「溶かす・流す・固める」という3つの基本工程から成り立っています。
- 1. 溶かす:プラスチック原料を加熱して溶融状態にします
- 2. 流す:溶融したプラスチックを高圧で金型に射出します
- 3. 固める:金型内でプラスチックを冷却し、固化させます
射出成形は、プラスチック成形の中で最もポピュラーな手法であり、さまざまな製品の製造に使用されています。金型を使用することで、同じ形状の製品を短時間に多数生産できる非常に効率的な方法です。その生産性の高さが最大のメリットとなっています。
射出成形の歴史と発展
射出成形の歴史は、19世紀後半にさかのぼります。1872年、アメリカのジョン・ウェスリー・ハイアットが、セルロイドを用いた射出成形機を発明しました。その後、1946年にジェームズ・ワトソン・ヘンドリーがスクリュー式射出成形機を開発し、現代の射出成形技術の基礎を築きました。
日本では、1950年代から射出成形技術の導入が始まり、高度経済成長期に急速に普及しました。現在では、日本の射出成形技術は世界トップクラスの水準にあり、精密部品や高機能製品の製造において重要な役割を果たしています。
射出成形機の構造と機能
射出成形機の主要部品
射出成形機は以下の主要部分から構成されています。
ホッパー | 原料のプラスチックペレットを供給する装置 |
---|---|
スクリュー | 原料を加熱・混練・送り出す装置 |
バレル | スクリューを包む円筒状の部品で、加熱シリンダーとも呼ばれる |
ノズル | 溶融したプラスチックを金型に射出する部分 |
型締め装置 | 金型を閉じ、射出時の高圧に耐える装置 |
金型 | 製品の形状を決定する重要な部品 |
射出装置と型締め装置
射出成形機は、主に射出装置と型締め装置の2つの主要な機構から構成されています。
射出装置
可塑化機構 | 成形材料をシリンダー内で加熱し溶融(可塑化)させます。 |
---|---|
射出機構 | 溶融樹脂をスクリューで押し出して計量し、型締めされた金型内に注入します。 スクリューの速度を制御し、一定量の溶融樹脂を押し出します。 |
型締め装置
型締め機構 | 金型を閉じます(型締め)。 材料の射出後、外側から冷却水で冷やし固化させます。 その際、樹脂が収縮し体積が減少するため、さらに材料を補給して金型内の圧力を保持します。 |
---|---|
突出し機構 | 成形品を金型から取り出します。 |
射出成形のプロセス
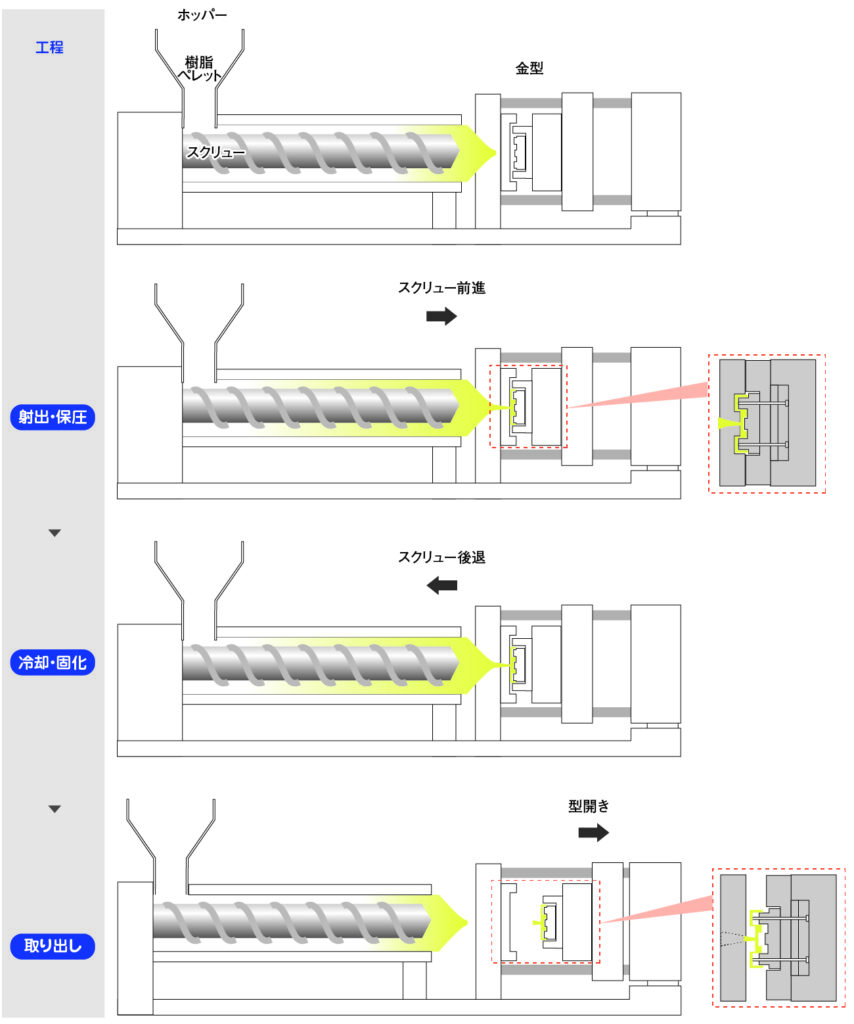
射出成形のプロセスは、以下のステップに分かれます。
1. 金型の準備
金型は射出成形において最も重要な要素の一つです。設計された金型が正確であることが、製品の品質に直接影響します。金型は通常、金属(主に鋼やアルミニウム)で作られます。
2. 原料の加熱と溶解
プラスチック原料(ペレット状や粉末状)がホッパーから射出成形機に供給され、スクリューによって加熱され溶融します。
3. 射出
溶融したプラスチックがスクリューによって高圧で金型に射出されます。このプロセスは非常に高速で行われます。充填圧力は、スクリューの回転数やシリンダーの背圧で調整可能です。
4. 保圧
射出後、金型内のプラスチックに一定の圧力をかけ続けます。これにより、収縮や変形を防ぎ、製品の寸法精度を向上させます。
5. 冷却と固化
プラスチックが金型内で冷却され、固化します。冷却時間は製品の大きさや厚さによって異なります。
6. 取り出し
固化した製品が金型から取り出され、次の製造サイクルが始まります。
取り出し工程における脱型不良を解消する方法については、『射出成形における品質管理と不良対策』で表面処理による解決事例をご紹介しています。
以上のサイクルを繰り返すことで、高速かつ効率的な大量生産が可能となります。
射出成形用の金型
金型の構造
射出成形の金型は、主に以下の部分から構成されています。
キャビティ | 製品の外形を形成する凹部 |
---|---|
コア | 製品の内側を形成する凸部 |
パーティングライン | キャビティとコアの境界線 |
ゲート | 溶融樹脂が流れ込む入口 |
ランナー | 溶融樹脂が流れる経路 |
スプルー | 射出ノズルから溶融樹脂が流入する部分 |
金型の種類
ツープレート金型 | 最も一般的な金型で、2枚の金型板で構成されています |
---|---|
スリープレート金型 | 3枚の金型板で構成され、ランナーの自動分離が可能です |
ホットランナー金型 | ランナーを常に溶融状態に保つ金型で、材料の無駄を減らせます |
ゲートの種類
ゲートの設計は製品の品質に大きく影響します。主なゲートの種類には以下があります
ダイレクトゲート | 大型製品に適しています |
---|---|
サイドゲート | 一般的なゲート方式で、多くの製品に使用されます |
ピンゲート | 小型製品や精密部品に適しています |
フィルムゲート | 薄肉製品に適しています |
ファンゲート | 幅広い製品に均一に樹脂を流し込めます |
関連記事:樹脂成形とは?基本事項から射出成形などの成形方法までご紹介
射出成形に使用される材料
射出成形に使用される材料は主に熱可塑性樹脂です。以下に代表的な材料を紹介します。
ポリプロピレン(PP) | 耐熱性と化学耐性に優れ、食品容器や自動車部品に使用 |
---|---|
ポリエチレン(PE) | 柔軟性と耐薬品性に優れ、包装材や容器に使用 |
ポリスチレン(PS) | 透明性が高く、食品パッケージや文房具に使用 |
ABS樹脂 | 耐衝撃性と成形性に優れ、電子機器や自動車部品に使用 |
ポリカーボネート(PC) | 透明性と耐衝撃性に優れ、CDやDVD、安全メガネに使用 |
ナイロン(PA) | 強度と耐熱性に優れ、機械部品や自動車部品に使用 |
ポリアセタール(POM) | 摺動性と寸法安定性に優れ、精密機械部品に使用 |
これらの材料は、製品の要求特性や用途に応じて選択されます。また、添加剤を加えることで、強度、耐熱性、難燃性などの特性を向上させることも可能です。
参考記事:熱可塑性とは?熱可塑性樹脂の特徴、種類、活用法を解説
射出成形の利点と課題
射出成形のメリット
1. 大量生産に適している
同一品質の製品を大量に生産するのに最適です。自動車部品や電子機器のハウジングなど、日常的に使用される多くのプラスチック製品が射出成形によって作られています。
2. 高精度な製品が製造可能
複雑な形状や細かなディテールを持つ製品も高精度で製造できます。これにより、部品の一貫性と品質が保証されます。
3. 材料の多様性
幅広い種類のプラスチック材料が使用可能で、特定の用途や機能に応じた材料選択ができます。
4. コスト効率
一度金型を作成すれば、その後の生産コストは低く抑えられます。大量生産においては非常にコスト効率が高いです。
5. 自動化が容易
射出成形プロセスは自動化しやすく、人件費の削減と生産性の向上が可能です。
6. 後加工が少ない
多くの場合、成形後の製品はそのまま使用可能で、後加工が最小限で済みます。
射出成形のデメリット
1. 初期投資が高い
金型の製作費用が高額で、少量生産には向いていません。
2. 設計の制約
金型から製品を取り出すための「抜き勾配」が必要なため、設計に制約があります。
3. 材料の無駄
スプルーやランナーなど、製品以外の部分も成形されるため、材料の無駄が生じます。
4. 成形不良のリスク
バリ、ヒケ、ウェルドラインなど、さまざまな成形不良が発生する可能性があります。
5. 大型製品の制限
非常に大きな製品の成形には、大型の射出成形機と金型が必要となり、コストが高くなります。
脱型不良の原因とその解決策について、実際に現場で成功した具体的な事例をチェックしてみませんか?離型コーティングを活用した改善の詳細はこちらから
射出成形における品質管理と不良対策
射出成形における品質管理は製品の一貫性と信頼性を確保するために不可欠です。主な不良と対策には以下があります。
不良の名称 | 現象 | 対策 |
---|---|---|
ショートショット | 金型内に樹脂が十分に充填されない不良 | 射出圧力の調整、ガス抜き、エア抜きの追加 |
バリ | 樹脂が金型の合わせ目からはみ出す不良 | 型締め力の調整、金型メンテナンス |
ヒケ | 冷却時の収縮による凹み | 保圧時間・圧力の調整、冷却時間の延長 |
ウェルドライン | 樹脂の流れが合流する箇所に生じる線 | ゲート位置の最適化、射出速度の調整 |
ボイド | 製品内部に生じる空洞 | 射出速度と圧力の最適化、材料の乾燥 |
そり・反り | 製品が平らでなく、曲がってしまう不良 | 金型温度の均一化、冷却時間の最適化、材料選択の見直し |
フローマーク | 製品表面に現れる流れの跡 | 射出速度の調整、金型温度の最適化 |
ジェッティング | 樹脂が金型内で噴射状に飛び散る現象 | ゲート設計の見直し、射出速度の調整 |
品質管理には、統計的プロセス管理(SPC)や自動検査システムの導入が効果的です。また、成形条件の最適化や金型設計の改善など、継続的な改善活動が重要です。
ヒケ、ボイド、ソリなどは、溶けた樹脂が冷却する際に起きるため、設計段階から成形品の肉厚を検討したり、金型温度の設計を見直す必要があります。一方で、脱型不良は成形条件や金型形状の見直し以外に、離型剤の使用や離型コーティングを活用することで解決できる場合があります。
特に、超耐久性フッ素系有機コーティングシステム バイコート®は、高い離型性と耐久性を実現し、脱型不良をはじめとする多くの成形課題を解決します。品質管理をさらに強化したい方は、ぜひ詳細をご覧ください。お問い合わせもお待ちしております!
射出成形の応用技術
多色成形・異材成形
異なる色や材質の樹脂(プラスチック)を組み合わせ、一体に成形する技術です。
2色成形 | 2種類の樹脂を用いて成形します |
---|---|
3色以上の多色成形 | 3種類以上の樹脂を用いて成形します |
異材成形 | 異なる材質の樹脂を組み合わせて成形します |
これらの技術により、複雑な色彩や機能を持つ製品を一度の成形で作ることができます。
インサート成形
金型にあらかじめ金属のネジや端子など(インサート品)を入れ、そのまわりに樹脂を注入し、一体に成形する技術です。電子部品や工具の製造に広く使用されています。
ガスアシスト成形
成形時に不活性ガス(主に窒素)を注入し、中空構造を形成する技術です。肉厚の均一化やヒケの防止に効果があります。
発泡成形
樹脂に発泡剤を混ぜて成形する技術で、軽量化や断熱性の向上が可能です。
化学発泡 | 化学反応で発生するガスを利用します |
---|---|
物理発泡 | 窒素や二酸化炭素などのガスを直接注入します |
マイクロ射出成形
極小サイズの部品を成形する技術で、医療機器や精密機器の分野で需要が高まっています。
高機能材料の射出成形
新しい高機能材料の開発が進んでおり、射出成形の可能性を広げています。
高強度・軽量材料 | 炭素繊維強化プラスチックなど |
---|---|
高耐熱性材料 | 自動車のエンジン周りなどに使用 |
導電性プラスチック | 電子機器のEMC対策に使用 |
生分解性プラスチック | 環境負荷の低減に貢献 |
射出成形と他の成形方法の違い
射出成形は、数あるプラスチック成形方法の中でも、特に汎用性の高い方法として知られていますが、他の成形方法と比較して、どのような違いがあるのでしょうか。ここでは、ブロー成形、押出成形、3Dプリントと比較しながら、射出成形の特徴を詳しく見ていきましょう。
ブロー成形との比較
射出成形とブロー成形は、どちらも溶融した樹脂を用いる点では共通していますが、その成形工程と得られる製品の特徴が大きく異なります。
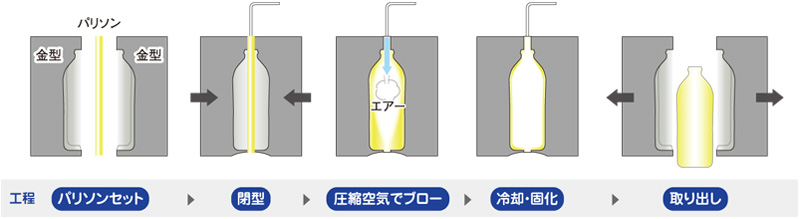
- 成形工程について
- 射出成形は、溶融樹脂を金型に高速で射出し、冷却・固化させることで成形します。一方、ブロー成形は、まずチューブ状のパリソンを成形し、それを金型内で空気圧によって膨らませて成形します。
- 成形品の特徴
- 射出成形は、複雑な形状や高精度な製品を成形するのに適しています。一方、ブロー成形は、中空形状の製品、例えばペットボトルや容器などを成形するのに適しています。
- 生産性の違い
- 射出成形は、一般的にブロー成形よりもサイクルタイムが短く、大量生産に適しています。
ブロー成形の課題解決に成功した具体的な事例をチェックしてみませんか?ペットボトルの透明性向上と作業効率アップの詳細はこちらから。
押出成形との違い
押出成形も、射出成形と同様に溶融樹脂を用いる成形方法ですが、その成形工程と成形品の形状に違いがあります。
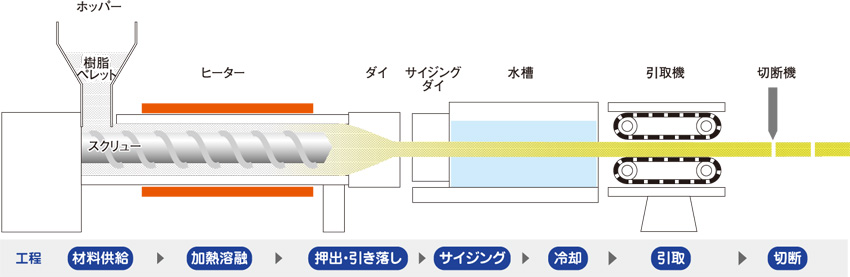
- 成形工程について
- 射出成形は、金型を用いて製品形状を決定づけるのに対し、押出成形は、溶融樹脂を一定形状の口金から押し出すことで、連続的に製品を成形します。
- 成形品の特徴
- 射出成形は、複雑な形状の製品を成形できる一方、押出成形は、パイプやフィルム、シートなどのように、断面形状が一定で連続的な形状の製品を成形するのに適しています。
- 生産性の違い
- 押出成形は、連続的に製品を成形するため、射出成形よりも大量生産に適しています。
押出成形での金型トラブルや製品不良を克服した具体例を知りたい方はこちら。生産効率を高めた最新の事例をご覧ください。
3Dプリントとの相違点
近年注目を集めている3Dプリントは、積層造形とも呼ばれ、樹脂などの材料を積層させて立体物を造形する技術です。射出成形とは、成形工程、生産性、コスト面で大きく異なります。
- 成形工程について
- 射出成形は、金型を用いて溶融樹脂を成形する一方、3Dプリントは、デジタルデータに基づいて材料を積層させて造形します。
- 成形品の特徴
- 射出成形は、大量生産に適しており、寸法精度や表面の仕上がりが良い製品を成形できます。一方、3Dプリントは、一品物や少量多品種の製品を、金型を必要とせずに製造できるというメリットがあります。
- 生産性の違い
- 3Dプリント3Dプリントは、金型が不要なため、初期費用は低く抑えられますが、材料費や加工時間がかかるため、大量生産には向いていません。一方、射出成形は、金型製作費がかかるため、初期費用は高額になりますが、大量生産によるコストダウンが可能です。
このように、射出成形は、他の成形方法と比較して、それぞれに特徴があります。
製品の形状、用途、生産量などを考慮し、最適な成形方法を選択することが重要です。
関連記事:樹脂成形とは?基本事項から射出成形などの成形方法までご紹介
まとめ
射出成形は、私たちの生活に欠かせないプラスチック製品を生み出す重要な技術です。自動車部品から家電、医療機器まで、その応用範囲は実に幅広く、今後もその重要性は増すばかりです。
基本原理は単純ですが、高品質な製品を効率よく作るには、材料選びから金型設計、成形条件の調整まで、細かな管理が欠かせません。生産工程の改善事例をお探しの方は、『成形工程から事例を探す』をご覧ください。さまざまな設備改善の成功事例を詳しく解説しています。
最近では、材料科学の進歩や製造技術の革新により、より複雑な形状や高機能な製品の製造が可能になってきました。
これからも、製品の品質向上や生産効率アップを目指して、射出成形技術は進化を続けていくでしょう。製造業の要となる技術として、産業界の発展に大きく貢献していくことは間違いありません。
私ども吉田SKTでは、射出成形金型への表面処理、特に離型処理を得意としています。多数の実績がありますので、成形のトラブルや金型へのコーティングでお悩みの方は、ぜひお気軽にご相談ください。詳しくは、『バイコート®(超耐久有機無機複合コーティングシステム)』をご覧ください。高い硬度と非粘着性を備え、射出成形金型に最適なコーティングをご紹介しています
また、私たちが提供する表面処理は、成形や包装工程の課題改善にも対応しています。詳しい情報やご相談は、お問い合わせフォームをご利用ください。弊社の技術営業員が個別にご対応させていただきます。